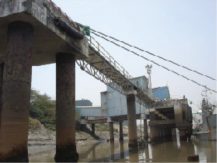
Jetty structure before strengthening
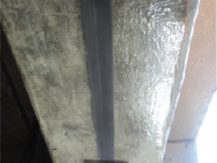
Fixing of carbon laminate to the beam at fixed anchorage end
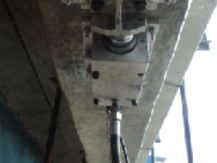
Pre-stressing of carbon laminate at mobile anchorage end
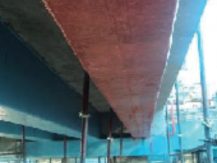
Beam after strengthening
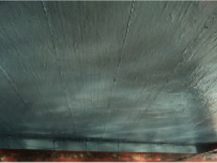
Slab after strengthening with carbon fibre wrapping
Make OR Break Factor
To effectively harnessing the high-tensile property of carbon laminates via pre-stressing
THE CHALLENGE :
- The main jetty and approach was suffering from a structural shortfall, due to the addition of a crane. It was also suffering from widespread corrosion in its steel reinforcements.
THE ODDS :
- The only scaffolding provided was suspended from the deck with anchors
- Tidal variations restricted work hours to 6 hours at a stretch, which necessitated the fabrication and use of quick-setting as well as moisture-sensitive materials
OUR RESPONSE :
- Our first step was to evaluate the reduction of strength due to corrosion. After which we did the following.
- Reanalyzed the design as per the additional requirements and designed a method of retrofitting
- We used micro-concreting to patch up the corrosion-damaged RCC members
- We reinforced the structural members with pre-stressed carbon laminates, carbon fibre wrapping and
glass fibre wrapping