
Residential complex under construction

Grouting the ports with different variants of monomers with varying spacing, saturation level and pressure (Location specific)
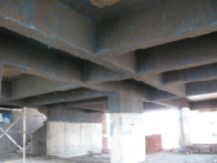
Beams & slab panels after completion of repair
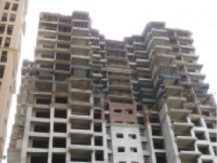
Construction work in progress during repair

Structure after 2 years of repair
Make OR Break Factor
Construction of the remaining 8 floors continued unabated with a floor being added every 20 days, the additional weights of which had to be factored in, into our retrofit method.
THE CHALLENGE :
- Stability of a residential high-rise was suffering from non-hydrated concrete that offered only 40% of its desired strength on the 15th and 16th floors.
THE ODDS :
- To facilitate work and the repair of external RCC members, we had to project scaffolding from the 15th and 16th floors of the building.
OUR RESPONSE :
- Post a detailed inspection of the structure, the cause of failure was analyzed and ascertained, and the following steps were taken:
- Trials were conducted on site, as we designed and modified material and methodology to achieve the desired strength
- Grouting and surface saturating of the RCC members with monomers was carried out
- RCC members were reinforced externally with a fibre wrapping system